Robotic Systems and Control
Introduction / English
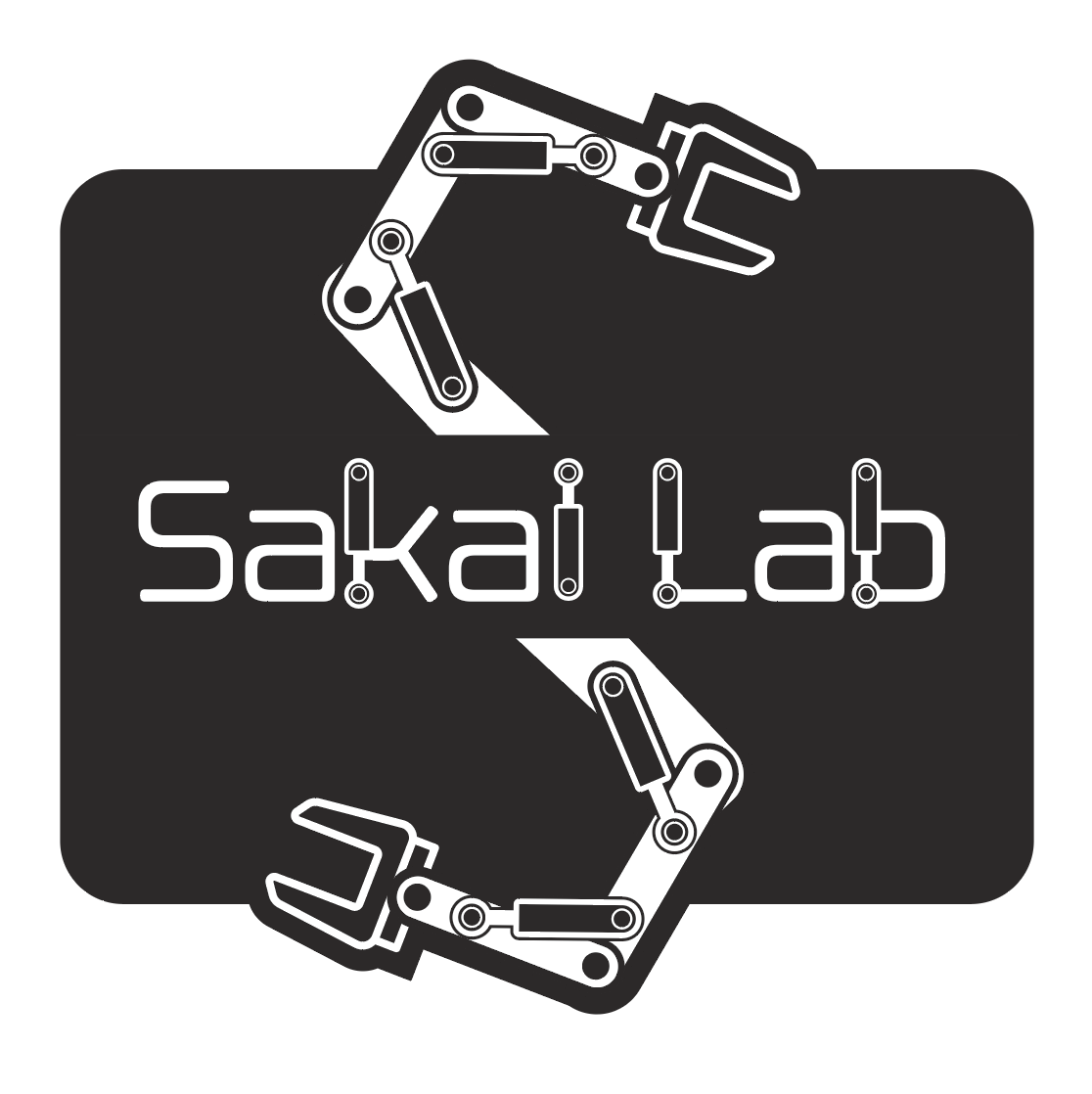
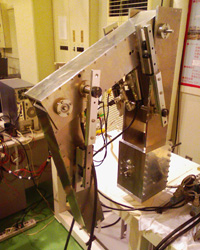
(The text below is for undergraduate students.)
Robotics is an incomplete field of study.
However, the question of whether or not robots can move freely goes beyond the scope of robotics and may affect the future of society as a whole.
Although we do not see these things in our daily lives, if painting or welding robots were to stop working, factories would come to a halt, cars and other products would no longer be able to be manufactured, and society would be in chaos.
Conversely, we often hear that assembly robots, which are also factory robots, are incomplete and do not work properly. Because they are not working, factories are being relocated from Japan to overseas, and foreign workers (foreigners) are assembling them.
Unlike painting and welding, assembly involves complex contact (orientation, position and force) of the fingers with the object and the environment, and the difficulty level of the problem is different.
Construction robots, nursing care robots, and agricultural robots are also (although this is misleading terms) not completed and not working, which is why workers (foreigners) are moving into the country from overseas. Construction sites, nursing care sites and farms cannot be moved out of the country like factories.
It goes without saying that if you look at the newspapers, the relocation and movement of these factories and workers is related to a wide variety of issues in society (such as students' job hunting activities).
On the other hand, if disaster relief robots and landmine removal robots, which are expected to be actively substituted, are completed and put into operation, it is likely that they will be able to save lives that previously had to be given up.
Here again, we cannot ignore the fact that the operating rates of the two are significantly different and develop them in the same way.
For these reasons, some (world-renowned) scholars in the humanities claim that robots today face the same situation as the eve of the development of the steam engine, which sparked the Industrial Revolution and dramatically changed society as a whole.
While the steam engine was a prime mover, a robot is a work machine, and the final question seems to be whether it will be successful as a general-purpose work machine, which operates on a different principle from dedicated work machines.
Specifically, in addition to the acute issue of saving human lives, the chronic problem of the intractable disease of mechanization (i.e., all tasks that are difficult to mechanize using dedicated machines and for which there are insufficient production units) must be resolved.
However, there seem to be many valuable themes in the process of getting there.
So how far has it been solved so far, and how successful is it likely to be?
In this point, a divide exists between robotics engineers and students, the media, and non-robotics researchers.
You can contact us (satorus@...) directly if you have an interest in our research. Our lab has some strong projects with big companies and European and American Universities.
If you are interested in robotics,
please check out the following "Yume Navi Lecture Video"!
「夢ナビ講義Video」
~SFの架空の大型ロボットを実用化するには?~
-
Hydraulic robotics (油圧ロボットと制御)
Our laboratory focuses on establishing model-based control (in the broadest sense).
Roughly speaking, model-based control is not a solution (skill) that works only for one robot (in a certain environment), but rather a solution (technology) that can be applied to all robots (ideally).
When the work environment is limited and unchanging, or can be taught to the robot as known, experimental model-free control is sufficient.
However, if this is not the case, experimental model-free control alone will result in an explosion of trial-and-error iterations, so theoretical model-based control is necessary and important.
To use an analogy, if the work of a palace carpenter based on experience is model-free, the work of an architect based on mechanics is model-based.
Using the new control principles discovered in our laboratory, we are focusing on establishing model-based control for hydraulic robots, including BigDog (while confirming the new effects through high-speed simulations such as the video below).
A new calculation method (video below) that can output the same calculation results in about 50% of the calculation time of the textbook method (video above).
-
Visual systems and control (視覚ロボットと制御)
We are researching a visual control method that does not use geometric features.(geometrical features)
(Not the inverted pendulum system used in university teaching around the world)
We are working on theories and experiments of visual control, focusing on free-surface systems as standard subjects. We are also applying this to unmanned vehicle systems.At first glance, the problem of robot technology appears to be sufficiently solvable by companies. In fact, robots such as ASIMO and Big Dog, made by companies, appear to move freely.
However, the difficulty of the problem changes dramatically depending on whether or not you ignore the fact that the work environment is variable and unknown. The point is that it is impossible to tell from the outside whether the robot is being ignored or not.
In other words, it is not possible to determine from a video or demonstration that shows a robot working in a certain environment whether tuning was repeated in a fixed or known working environment. (And in fact, you can't tell by looking at a robot only from the inside. Even if you look into the robot's computation program, the model is usually not described. Recently, it seems that an increasing number of astute students are beginning to realize that visualization, such as videos and demonstrations, is necessary but not sufficient..)In this research, we are developing a new visual control method from the standpoint of model-based control, which does not separate the visual processing computer from the motion control computer as in ASIMO, and is suitable for cases where the working environment changes or is unknown and cannot be taught to the robot.
-
Agricultural robotics (農業ロボットと制御)
Hydraulic robot that can control arm and vehicle directly from visual information (Unlike ASIMO and many other full-body robots from other universities and companies, this robot does not "separate" the computer for control calculations from the computer for image processing, so hydraulic robot capable of new whole-body motion control utilizing the original freedom of computers
Watermelon harvesting robot (high speed mode)
Mechanical hand that can grasp and release despite the absence of electrical and electronic parts, including sensors and motors (only mechanical parts are used, making it resistant to harsh environments and reducing electrical-related costs )
A vehicle that transforms from a helicopter to an airplane