有機半導体や新しいナノ材料を用いて薄膜作製に必要な温度や時間を劇的に減らすことが可能です。
例えば、製造に要する加熱温度や時間を500~1000℃で何時間も要したものを100~150℃で数分に短縮したり、製膜時間を数100秒からたったの2~3秒に減らして大面積化も可能とするとどうなるでしょう?
(i) 製造に必要なエネルギーは1/100以下
(ii) 装置装置は巨大な真空装置などの1/10以下で導入で来て生産能力は100倍。
つまり製造コストが1/100以下になって環境にも財布にも優しいモノづくりが実現可能。
また、分子や光の性質を利用して厚さ10nm以下の極薄の絶縁層と有機半導体分子膜の2層膜をインクを特殊な条件で塗布するだけで自発的に、VUV(深紫外)光を照射したところだけにパターン形成形成可能です。
その結果、これまで工程に3~4時間を要していたのが、わずか5分以内で完了して、デバイス性能は従来素子を上回ります(低電圧動作&高移動度を実現)。
加えて、新手法では100℃以下で製造することも可能となりフィルム上にも作製可能となります。
このような製膜技術を使ってガラス板のような硬いものに加えて、サランラップやPETフィルム、
あるいは薄い紙のような柔らかい物の上に自在に有機トランジスタ、メモリ、発光デバイス、センサなどに作製できるようになれば・・・
次世代のエネルギーハーベスティングやディスプレイ、電子装置、さらには、身体に貼り付けて動作する医療デバイスの可能性が大きく広がると考えられます。冗談抜きで。
【実は1gあたりでは高い高性能有機半導体や半導体量子ドットを薄く無駄なく活用する。ペロブスカイトのPbやCdなどの消費量を極限まで減らす。】
高効率な有機太陽電池や発光素子の材料は1gあたり数10万円なんてものが多くあります。
(注;これは研究開発用の材料の話ですので、実用化段階では量産することで1/10以下になりそうですが、それでも 1g 数万円はしそうです。)
例えば、比重が水と同じ1として1g の材料から厚さ1μm(=1000nm)の膜を製膜すると材料を100%利用したとしても、1m2にしかなりません。AgやAuのように比重が10を超えるような重い無機物質であればA4用紙1枚分の面積くらいにしかならないため非常に高くなります。スピンコート法では、これほど高い材料を9割以上捨ててしまうので、大変もったいない事態になりますね。おそらく、普通の人には手が出ません。
けれども、10nmの厚さで無駄なく半分以上をデバイスに活用すれば、たった1gから畳50個分くらいの面積に広げられ、畳やふとん1枚の面積で1000円台になる可能性があります。
貴重な材料あるいは環境に影響がありそうな材料を薄く、無駄なく(廃棄しない)、きれいに、しかも素早く製膜して重ねることができて初めて
近い将来、皆さんが手軽に利用できたり、ビニールハウスや窓、壁、鞄や衣類など身の回りの様々なものに貼って使えるモノづくりが実現すると期待します。
伊東研では、新しい塗布製膜技術や転写などの積層技術と適宜真空プロセスを組合せてより安心・安全、財布にも優しいデバイス製造技術の開発と高性能化を同時遂行して、環境問題に貢献します(目標)。
- 研究テーマ
伊東研究室では、誘電体薄膜、有機半導体やナノシート、量子ドットなど厚さや大きさがナノメートル(10億分の1メートル)サイズの新材料を組合わせた
「ナノ分子エレクトロニクス」の発展に貢献します。
*太陽電池や有機EL・量子ドット発光ダイオード、コンデンサ、次世代のメモリーデバイスやセンサー等の高性能化と動作のしくみを調べる研究をしています。
工夫次第で桁違いの時短と簡便さで製膜できる塗布 (=ウェットプロセス)技術と真空プロセスを組合わせて驚異的な性能と新機能を発現する次世代デバイスの実現を目指して、新機能の発現や高性能化のしくみを調べながら自身も含めメンバー全員の成長を目指しています。
- 有機エレクトロニクスとナノ分子エレクトロニクスの発展
1980年代までの長い間、有機材料は主として電気絶縁材料として用いられてきました。
現在でも、電力ケーブルの絶縁技術や、集積回路の基盤としてあるいは層間絶縁層には誘電率が低く絶縁性能の優れた高分子(樹脂系)の絶縁材料が使われています。
1980年代後半に有機半導体を用いた薄膜太陽電池やトランジスタ、発光デバイス(有機EL (または通称 OLED(OはOrganic=有機))が提案され有機エレクトロニクスという研究分野がスタートしました。
実用面でも1990年代頃より、液晶デバイスがディスプレイの主役となり、さらに2010年代末には有機ELがディスプレイの双璧となり、今やテレビやスマートフォンなどのディスプレイの殆どが有機デバイスと薄膜トランジスタで作られています。
これらの発展は、従来のSiの概念を踏襲しつつも、無機材料には無かった有機分子ならではの基礎的物性の解明や新規の高性能材料の開発によるものであり、材料のさらなる発展とその機能を最大限応用するための自由なアイデアが道を拓くと考えられます。
有機材料だけではいろんな夢の実現は難しいけども、厚さや太さがナノメートルオーダーの炭素材料や金属・酸化物・量子ドットと呼ばれる化合物半導体と有機材料を低温技術で組み合わせるナノハイブリッド技術の発展により、ウルトラ軽量でフレキシブルなディスプレイや発電装置やセンサシステムなどが現実のものとなる時代にいままさに突入しようとしています。また、半導体集積回路のロードマップを参考にすると10年後は分子1個分の大きさにメモリーや演算能力を搭載させたデバイスが現実になる時代が到来しそうです。
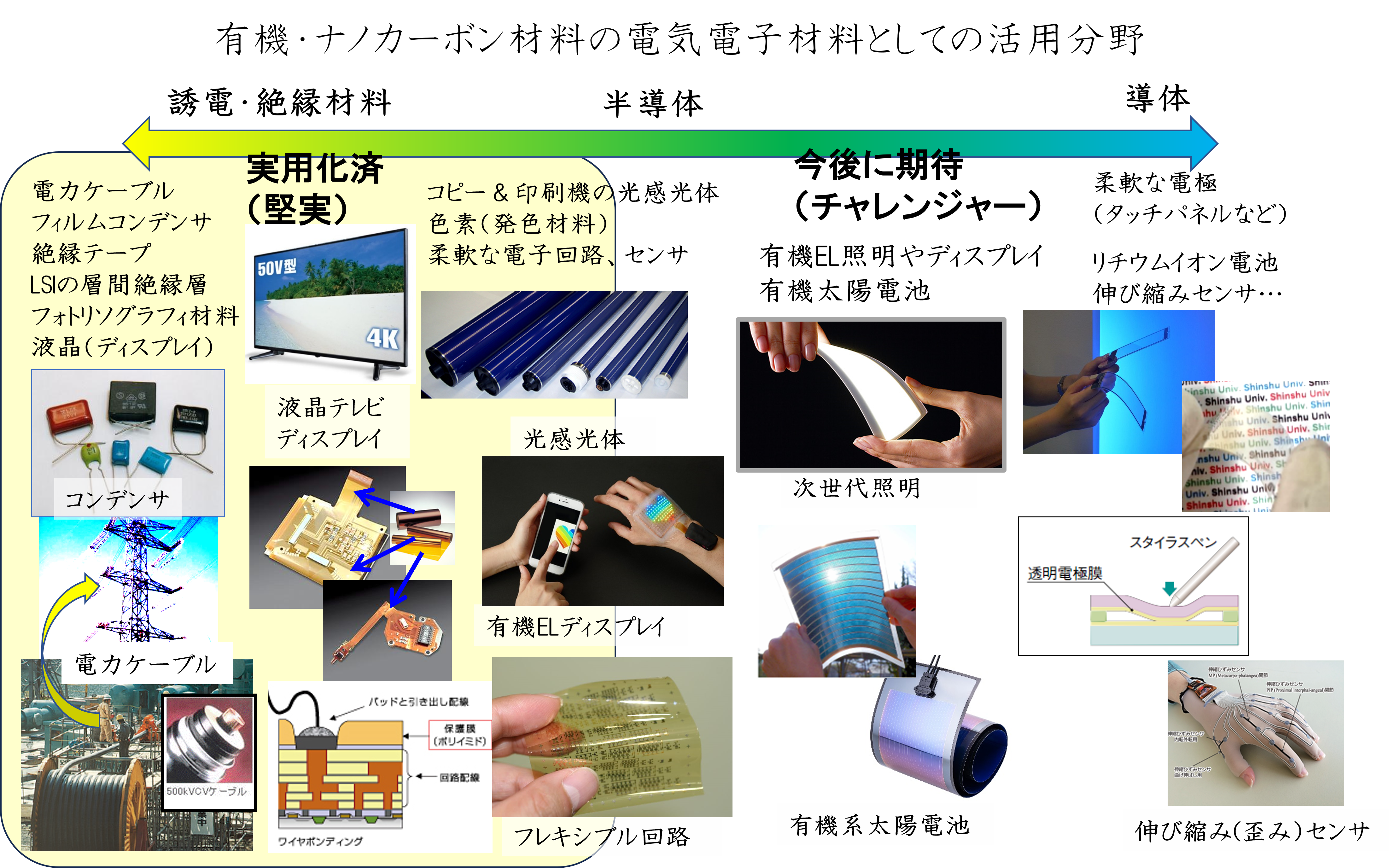
以下にいくつかトピックを紹介します。クリックすると、詳細を御覧いただけます。
※怠けていましたが2025 Feb.に更新したのでぜひご一読ください。
逆構造の有機EL(OLED)
有機EL(または Organic Light Emitting Diode: OLED) がテレビやスマートフォンのディスプレイ素子として主流になってきています。
新しい材料やデバイス技術のおかげで効率も良くなって省エネでキレイですね。プラスチックフィルムなどの上に作製すれば超薄くてフレキシブルにもなります。
但し、OLEDやLEDは水や酸素の近くで発光すると化学反応して壊れてしまうので封止しないといけません。
通常(順)構造は低い電圧で動作できるが不安定な金属を上部電極に用いるため厳密な封止が必要なためガラス板を貼り付けますが、 上部電極を大気安定なAgや(ちょっと高いけど)Auとして電流を流す向きを上下反転した「逆構造型」は封止レベルが下がりバリア性のフィルムで封止可能になるため フレキシブル化に有利であることがNHK技研など多くの期間で実証されています。
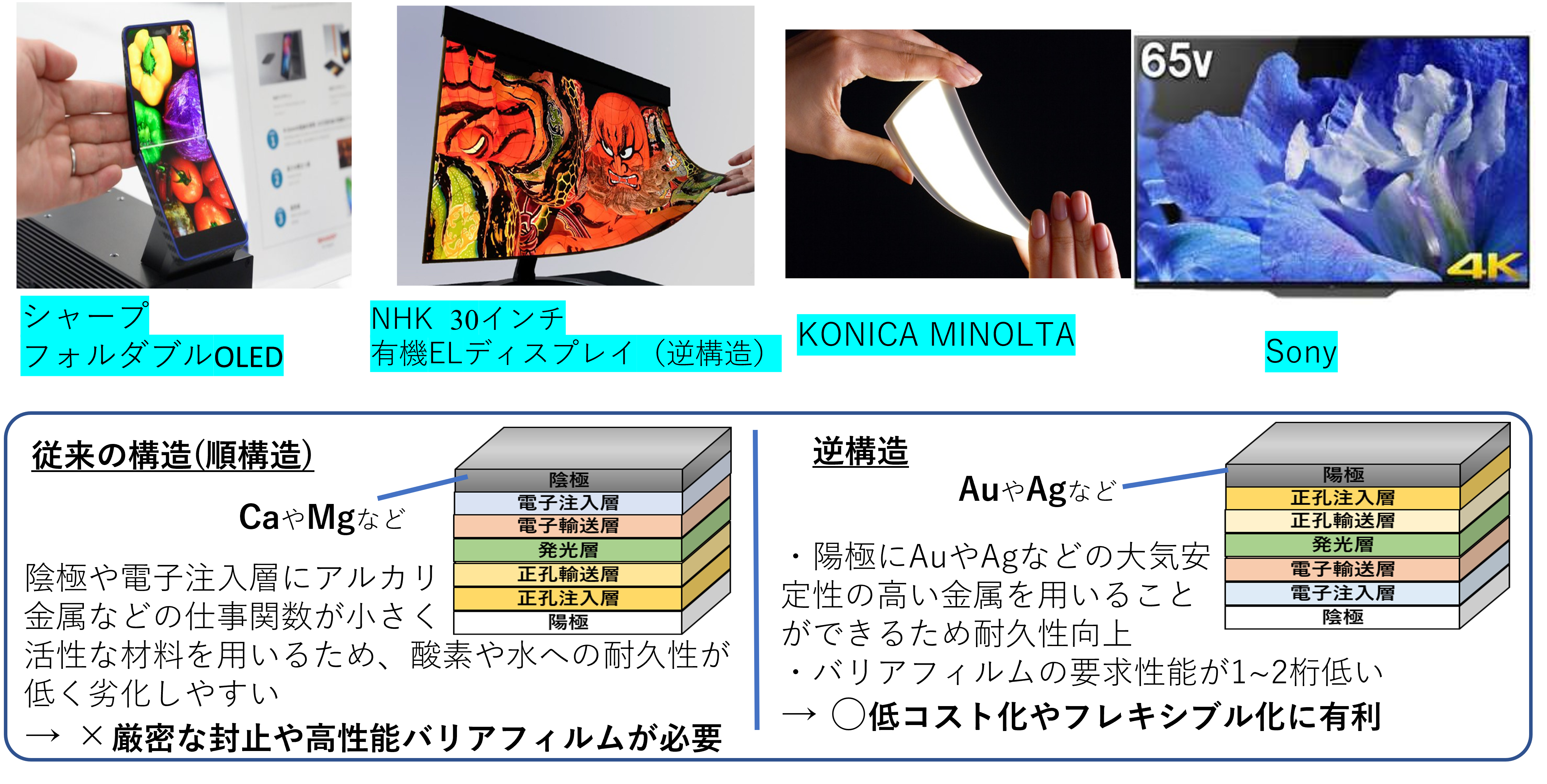
そこで、伊東研では逆構造型の青色または白色OLEDの開発と高性能化に取り組んでいます。しかも、塗布型で。でも、何故塗布型なんでしょう?
現在、ディスプレイ用の有機ELは透明電極の上に厚さ10nm台の薄膜を10層近く積層して作られます。 有機ELテレビは幅が 1 m を超えますが、このサイズを蒸着するには直径数mの巨大な真空装置を真空を破らずに10台近く連結するので装置が体育館なみに巨大化します。
有機膜の蒸着レートは 0.1 nm/s前後で1層の製膜に1~10分要するので1日数100枚の製造能力しかないためどうしても高くなります。
また、有機ELの照明応用が期待されますが、 LED照明に比べると電流密度が1/10000位なので発光面の面積を数100mm角(1万倍)に 大きくして優しく光るのが有機EL照明なので、大面積の発光素子を1日数1000~数万枚のペースで1/10以下の価格で作ることが求められるでしょう…
前の項目で紹介した塗布型技術ならば製膜時間を10秒前後に短縮可能であり、 大面積化しても装置のコストは1/10以下に収まるので生産能力は100倍、コスト1/100が可能となります。
塗布型の白色OLEDの実現は明るくて優しい照明実現の要と考えられます。
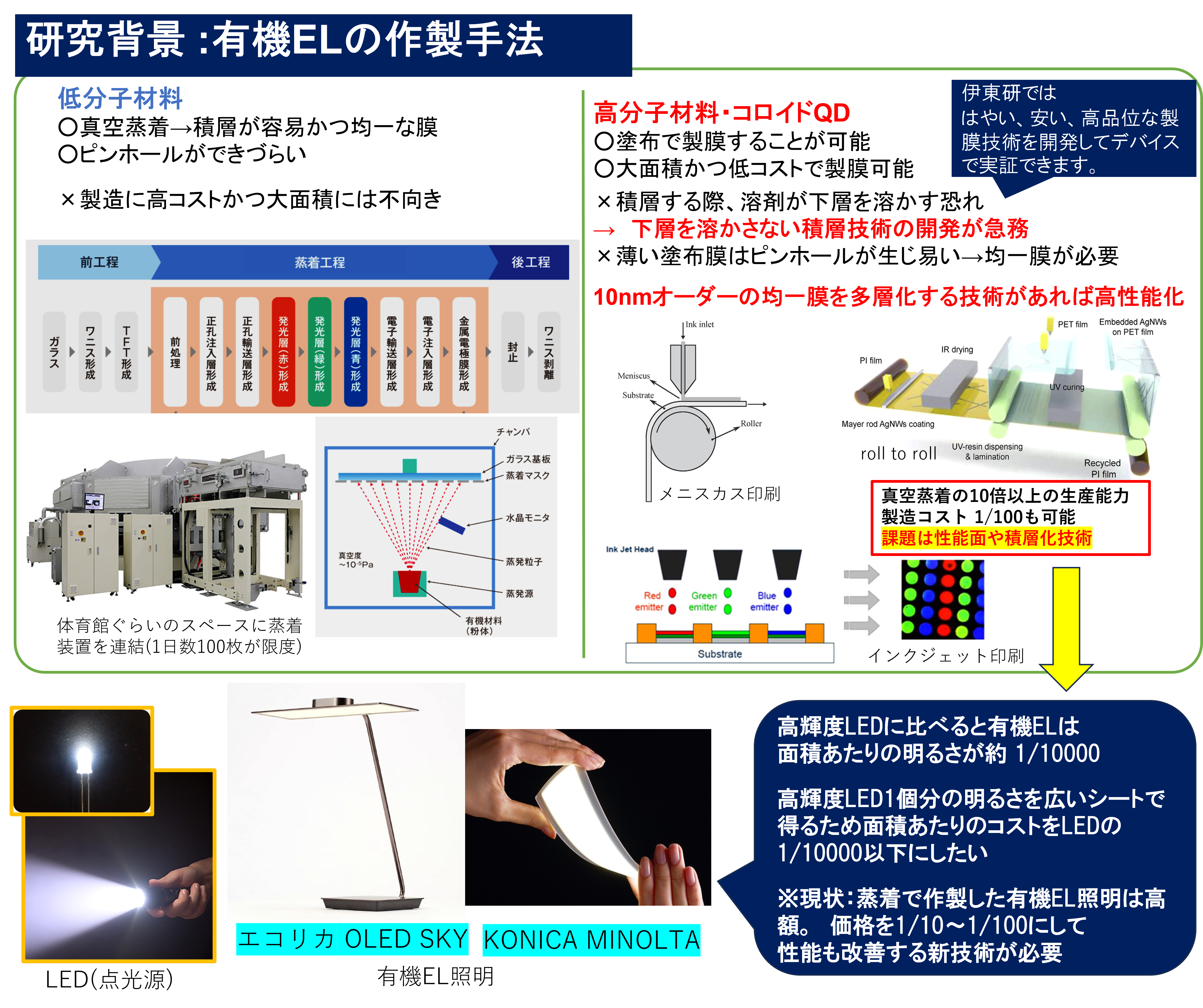
しかし、性能面で現状は大きく劣るため、伊東研では低電圧で明るく光る高性能な塗布型OLED(逆構造型)の研究開発を進めています。 そこで、伊東研では「塗って(低温で)製膜出来て、発光層も塗り重ねOKな電子注入層の開発と、低電圧で明るく動作する逆構造OLEDの開発」を進めています。
全塗布型で積層構造を得るのも、それで発光効率を得るのも最初は簡単ではありませんでした。少しずつ改良を重ねて最初は 10 V を超えていた動作電圧を 6 V さらに 2024年度は3V以下(青色OLED) まで低減しており、EQEも改善しています。ようやく、実用化するならこれくらいの性能といったものが視野に入りそうです(^_^)
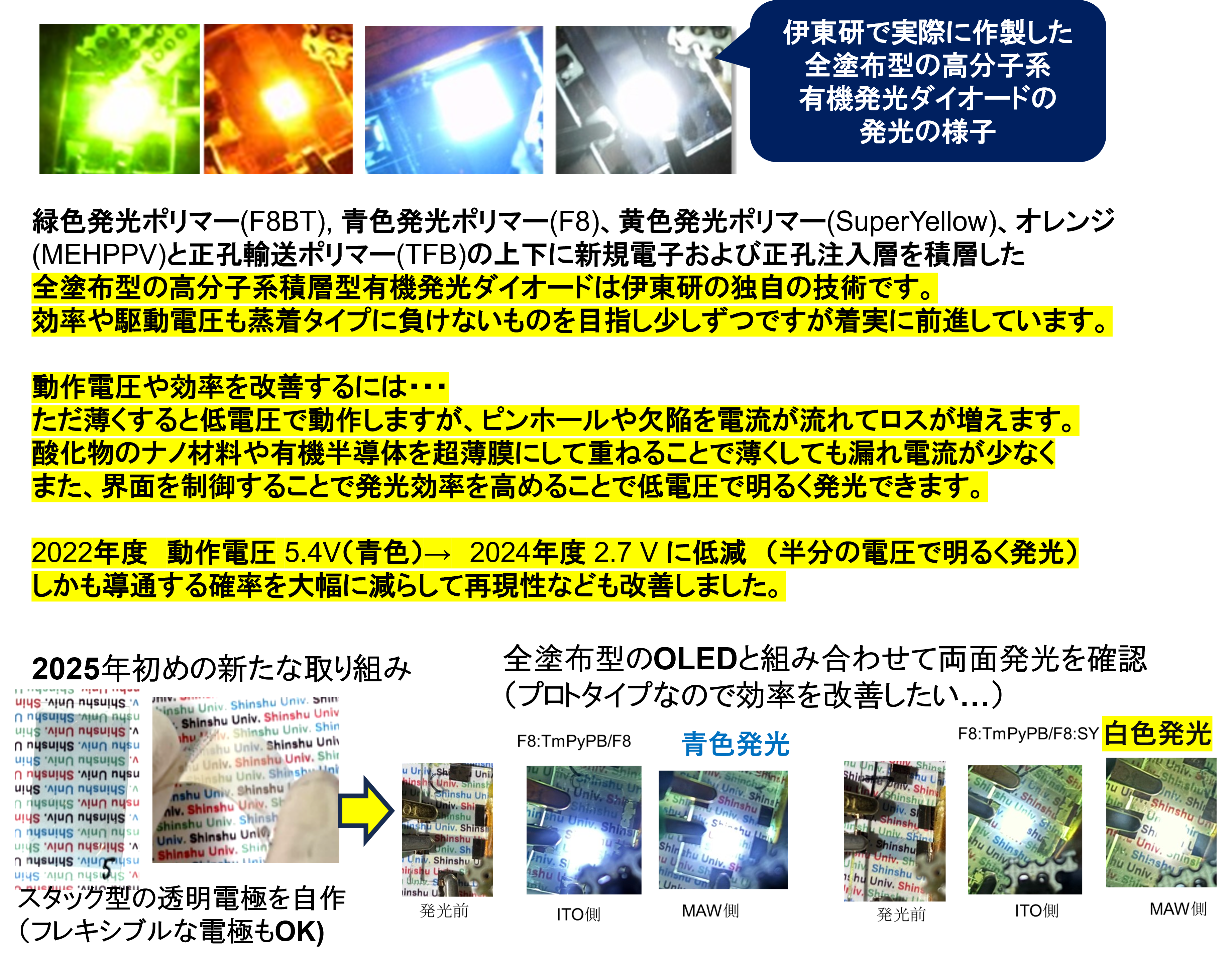
逆構造の量子ドット発光ダイオード
2023年のノーベル化学賞の受賞対象でもある半導体量子ドット。
これを発光層に組み込んだ次世代発光尾素子が量子ドット発光ダイオードで多くの性能面でOLEDを超える可能性があります。
上記のように、逆構造のOLEDは電子注入が課題であるが、逆に発光材料を中央(Core)にCdSeやCdSあるいはZnSeを配置し その周り(Shell) ZnSなどのバンドギャップが大きな半導体で囲んだ半導体量子ドット(Quantum Dots: QD ) をOLEDの発光層に置き換えた場合は、 伝導帯が深い位置にある(=電子親和力が高い)ため、電子を容易に注入出来て電子輸送性の方が高い、逆に正孔の注入と輸送が課題であるといった特徴があります。
実はQDは塗布法で製膜するしかありません! つまり、塗布型の逆構造OLEDとの相性が良く、改良したOLEDの構造と殆どそのままで発光層の部分を置き換えると低電圧で、美しく・しかも低電圧で発光します。
青色QDは耐久性の面で青色有機ELを超える可能性もあり、伊東研では発光層を半導体量子ドット(QD) と高分子のブレンド膜とした逆構造のQLEDの研究を進めています。
現在、オレンジや緑色の発光素子では 2 V 程度で発光し、青色で2.9 V発光する素子が得られていますが、大電流で効率が減少しない工夫(Roll-off問題)や、 EQEのさらなる向上と全塗布で低電圧&高性能をスローガンに研究を進めています。QDをブレンドした発光素子の特徴は以下のようになります。
・〇発光材料の中でQDは最も色純度が高く、理想的な色再現が可能となる。
・〇低電圧動作が可能で耐久性と効率向上も期待できる。
・◎? 塗布で製膜(真空プロセス不可)→塗布型の逆構造型OLEDとの相性抜群。 ・× 材料が極めて高額:有機発光材料と比べるとかなり高いが、無駄なく、10 nm(QDの直径程度)に薄く製膜できれば解決できる。
・× 金属や酸化物から距離を空けないと効率よく光らない:積層構造を工夫して発光層の位置を制御する手法(逆構造OLEDの技術の発展版)が有効
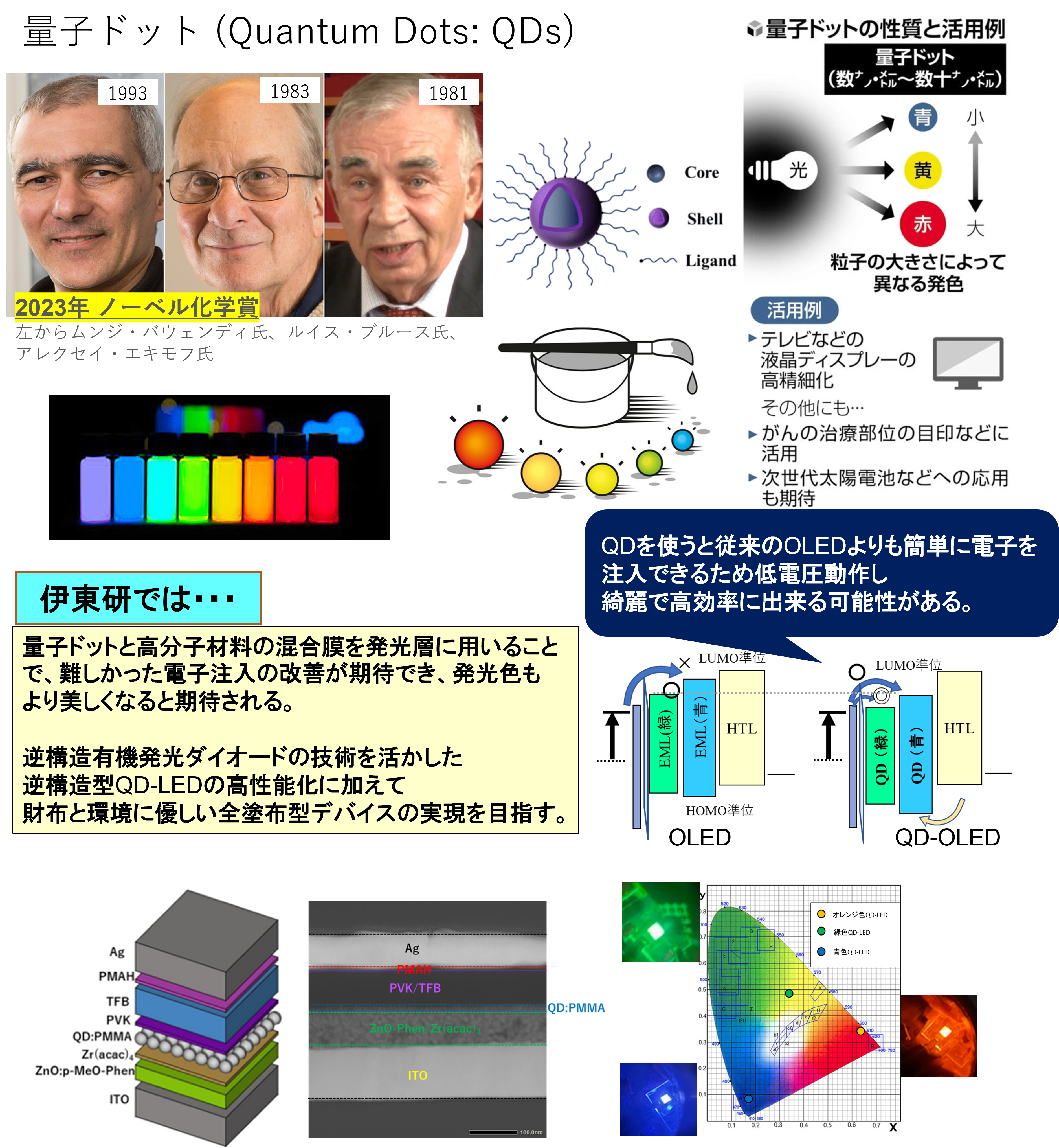
これらは環境発電デバイスあるいは、小型の発電という意味でマイクロ発電デバイスなどとよばれます。太陽電池もその一つで、例えば太陽光に比べると室内の蛍光灯やLEDの光の強さは1/100にも満たない可視光で構成されますが、有機太陽電池やペロブスカイト太陽電池は屋内光に対する効率が太陽光の1.5倍かそれ以上になるなど、こうした応用でさらなる真価を発揮します。ただし、太陽光が真昼の晴天時で100 mW/cm2 ですので、室内光は 1 mW/cm2 以下となるので、 1cm角程度の面積で発電する電力は高々 10-4W/cm2 しかありません。
これと同程度か超えるエネルギーとなるのが、振動発電や摩擦発電になります。振動発電の例として圧電材料や磁歪材料が挙げられますが、セラミックの圧電体は衝撃に弱く飛んだり跳ねたりすると割れて壊れてしまう欠点があります。磁歪材料は大面積化やコスト面で課題があります。
これに対して、ポリフッ化ビニリデン(PVDF)に代表される強誘電性や圧電性を有する高分子(もちろん有機膜)、あるいは極性基を持つ高分子(ポリマー)に最初に少し温めて電圧を加えて分極処理を行うと、室温で分極状態が保持されます。材料によっては、製膜するだけで自発的に電位を形成して大きな電圧を発生する有機膜も存在します(Giant Surface Potential: GSP)。これらを、踏んでへこませたり、曲げて変形させたり、くねくねさせると電気エネルギーを発生します。
高分子フィルムはμmオーダーの厚さでも、電圧を出力するため、何枚も重ねて変形することで、より大きな電力を発生し、衝撃に強く割れないので、大面積化することで大きな出力を得ることが可能です。 この他にも、フィルムの表面にナノ材料を配置して摩擦すると太陽電池に負けない出力が得られることも見出されています(通称 TENG)。ただし、固体のナノ材料の摩擦は摩耗し易いという欠点もあります。
安くて高性能で安全な水滴発電デバイス
こうした中で、最近は、水滴発電デバイスなども注目されています。
いわゆる雨滴(雨水:直径 1~6 mm 程度の水滴)をフッ素系高分子のPTFEや Cytopに滴下する際に、水とフッ素膜の間の摩擦帯電により水が正に帯電してフッ素膜が負に帯電しエレクトレットとなり、その後はさらに帯電が進むと同時に、帯電したフッ素による静電誘導で水中のイオンが分極(移動)して反対側のキャリアが電極から取り出されて発電します。 誘電体薄膜を改良すれば、さらなる高性能化が期待できるほか、雨水や海水は場所によっては無限に供給可能なエネルギー源となる可能性があります。
さらに、近年はフッ素化合物の規制が厳しいうえにフッ素樹脂は高いので、フッ素樹脂の使用量を他のグループの1/100以下で安く安全で性能でも勝てるよう改良しています!
このように、ナノ材料や有機分子で表面をコントロールしたり、軽量化・柔軟性を持たせた、有機誘電体薄膜は軽量でしなやかで大面積化も容易な実用的で 楽しい環境発電デバイス実現の可能性を秘めています。
伊東研では有機誘電体薄膜や酸化物の薄膜を組み合わせた、新しい発電デバイスの開発も手がけています。
2022年度から手がけた研究ですが、3年間で出力は1000倍に向上し水滴が流れるだけでLEDの発光を確認できるまでになりました。
性能はもっともっと向上できそうです。これからの研究の一つの主役かもしれませんね。
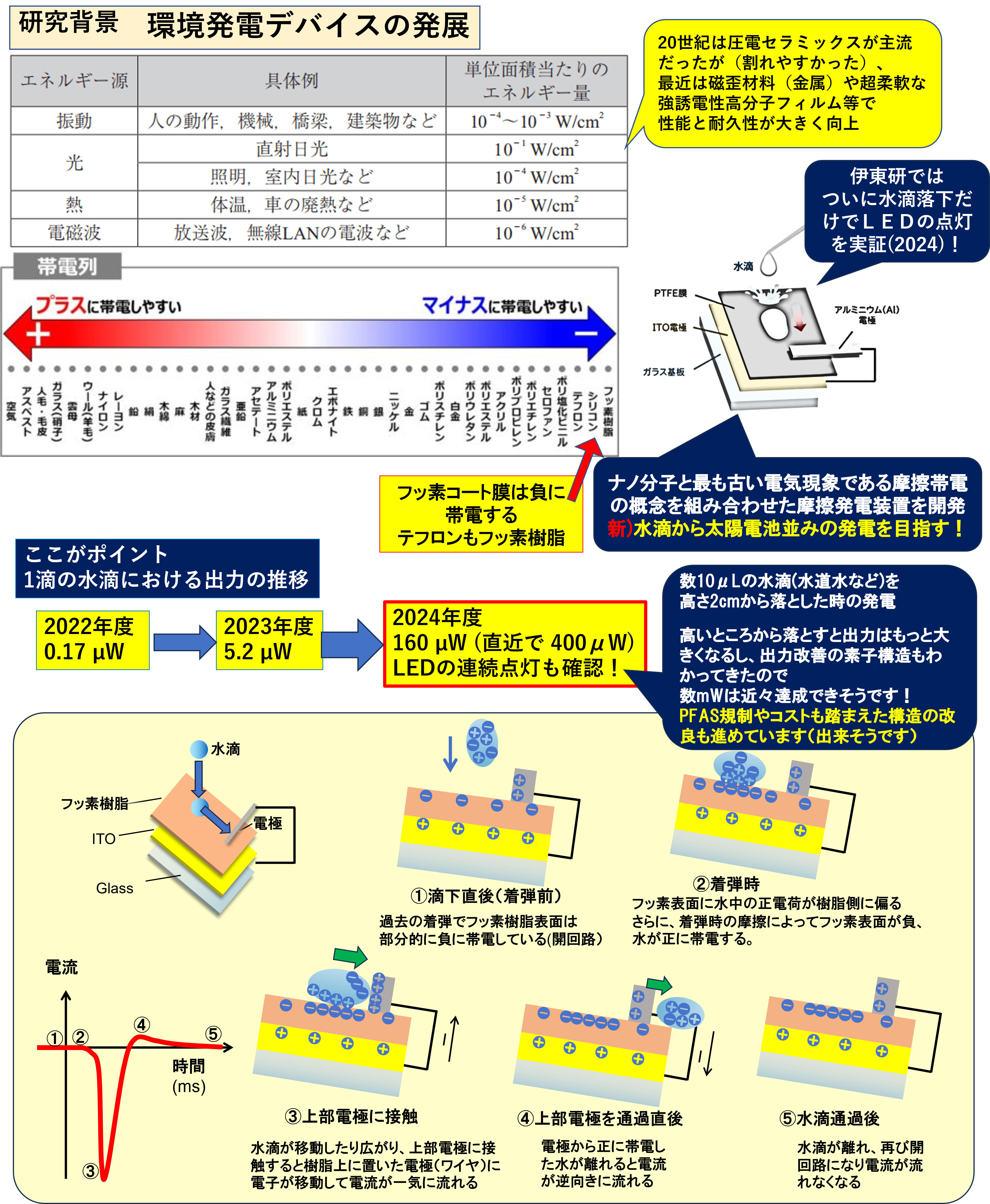
1980年代まで 1 %にも達しなかった有機系薄膜太陽電池の電力変換効率は、色素増感型太陽電池、バルクヘテロ接合型有機薄膜太陽電池、ペロブスカイト太陽電池の登場と、 特に2010年以降の材料・デバイス技術の発展により、有機薄膜太陽電池とペロブスカイト太陽電池ではSiと双璧をなす20%を超える例が次々と報告されています。 これら有機系薄膜太陽電池ならではの低温・塗布プロセスや、柔軟なフィルム基材上の作製と実用化が進むことで様々な応用展開が期待されます。
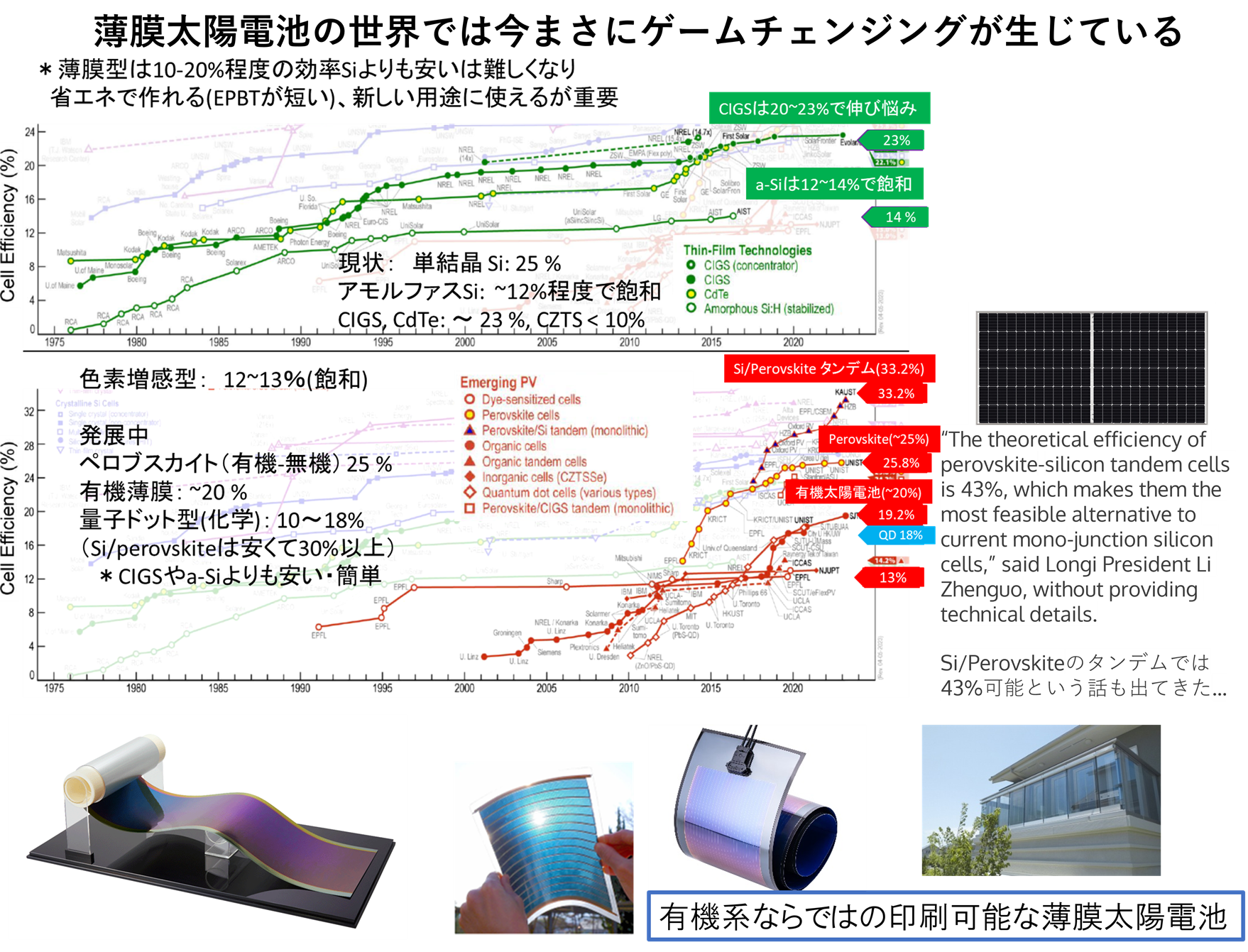
有機薄膜太陽電池
伊東研では、逆構造のバルクヘテロ接合型有機薄膜太陽電池の研究を進めてきました。
「逆構造」は「順構造と上下が逆」で、下部電極上に電子バッファー層を配置し、活性層、正孔バッファー層、上部電極の順に積層した構造となります。AgやAu(Auはちょっと高いので実用化に難がありますが・・・) など安定な金属を配置することで、大気安定性が増します。
「順構造」では電子を取り出しやすいように仕事関数が小さな金属(例えば、Al、Mg、Caなど)を上部電極に使いますが、大気中の水や酸素とすぐに反応して劣化するため これを防ぐために、ガラス板や吸湿剤を組み合わせてデバイスを覆う必要があり軽量化や低コスト化の弊害となります。
フィルム上に作製していろんなところに貼って使う特徴を考えると、「逆構造型」が有効です。
そこで、伊東研究室では、「逆構造型」のバルクヘテロ接合型(bulk-hetero-junction: BHJ)の有機太陽電池に着目しています。
また、有機系太陽電池は光電変換材料や様々な酸化物のナノ材料を積層して作られるため、ナノ分子材料を10nmオーダーで薄く均一に素早く製膜する技術が実用化(低コスト化と高性能化の両立)に重要です。
バルクヘテロ接合型太陽電池は最初は真空蒸着膜を用いて平本先生らにより提案されましたが、 その後、n型のフラーレン誘導体とp型高分子のポリチオフェン誘導体(主にPCBMとP3HT)をトルエンやクロロベンゼンに一緒に溶かして塗るだけで 3~4%の電力変換効率(PCE) が実現できるようになり、 塗布型の太陽電池に注目が集まるようになりました(1990年代後半から2010年代)。 その後、赤から近赤外領域に吸収帯を持つドナー/アクセプタを合体させたバンドギャップの小さなp型半導体の登場でPCEが10%前後のBHJ太陽電池が登場し、 2010年代末から2020年代には非フラーレン型のアクセプタ(n型半導体)(通称 NFA)が台頭し、p型にPM6を用い n型に代表的NFAであるY6等を用いてシングルセルで15~18%の太陽電池が登場しています。
しかし、これらの半導体は(あくまで割高の研究開発用ですが)100mgで10万円もして、今後量産すれば安くなるとは言え、超薄く無駄なく綺麗に大面積に製膜する技術が大事になりそうです。
伊東研でも、一時は諦めかけたBHJですが、 前項の「環境と財布に優しい、低温・塗布形成の高性能デバイスの開発」が活躍しそうです。 これまでに培った、酸化チタンナノシートなど1nmの薄さで厚さ制御可能で、100℃以下で塗布プロセスで簡便に製膜可能かつ平坦な2次元半導体や、 酸化亜鉛ナノ粒子+ナノ平坦化層を有する技術や、薄く速く綺麗に積層する技術を用いた逆構造BHJ太陽電池の開発を検討しています。
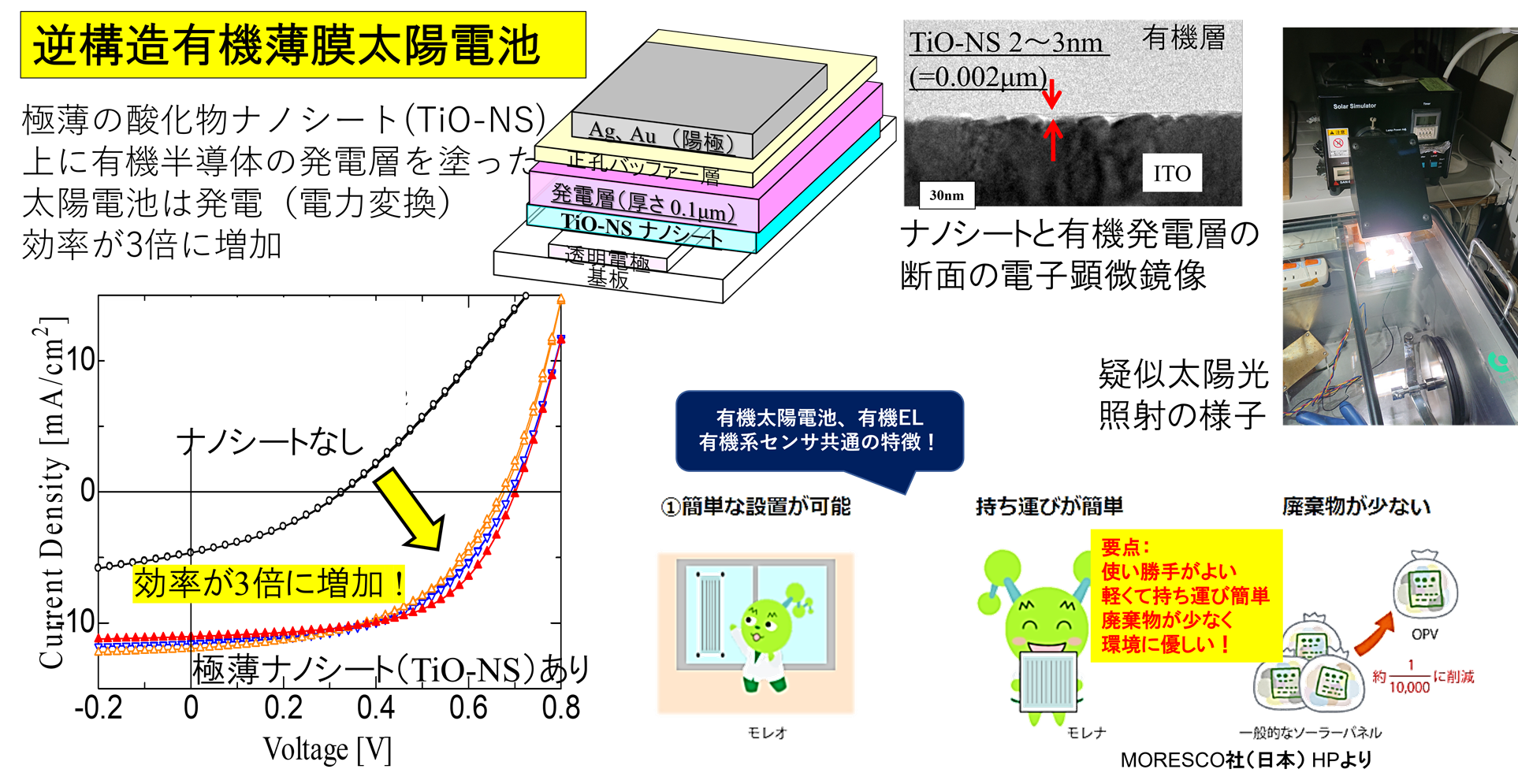
ペロブスカイト太陽電池
ペロブスカイト太陽電池は、日本の宮坂先生によって発明された太陽電池で、 最初は色素増感型太陽電池の流れで(後に別物であることが判明しましたが)開発されました。 (詳細は、宮坂先生の著書「大発見の舞台裏で!ペロブスカイト太陽電池誕生秘話」や論文をお読みください。) ペロブスカイト太陽電池は、今や塗って作れる簡単・大面積・低コストな技術でありながらも Siに負けない性能を実現しており、薄膜太陽電池業界の中心となっています。 Si太陽電池と積層した「タンデム型」では34%も報告されており、この流れはゆるぎないものとなりつつあります。
少し、ややこしいのですが、色素増感型太陽電池からの流れで有機太陽電池でいうところの「逆構造」がペロブスカイトでは「順構造」になり、「有機の順構造」が「ペロブスカイトの逆構造」となります。
伊東研究室では「全塗布型の逆構造のペロブスカイト太陽電池」の研究を行っています。
順構造ではまず、酸化チタンや酸化スズを塗布→数100℃で焼成して結晶化→発電層(ペロブスカイト層)→正孔輸送層→(必要により正孔バッファー層)→上部電極の順に製膜します。 酸化チタンと発電層の界面の欠陥がヒステリシスや不安定化の温床になることや、正孔輸送層の多くが導電性が不十分で Liイオンなどをドープするため耐久性に影響する点や、 上部電極に高いAuを用いることが多く、コストや安定性、低温プロセス(フレキシブル化)の弊害となります。
一方、伊東研が注目する逆構造では、まず ITOなどの透明電極に正孔を選択的に取り出す自己組織化単分子膜を形成します。 厚さは分子1個分で非常に薄いのでドープ不要で欠陥も無くせるためヒステリシスも抑制します。しかも100℃以下で製膜可能です。 その上に、発電層のペロブスカイト層を製膜し、電子輸送層や電子バッファー層を製膜し、上部電極を形成します。
一つ前の項目の新しい塗布法と積層化技術により、懸念材料であった電子輸送層やZnO電子バッファー層の消費量を1/10以下でしかもきれいに積層します。また、ペロブスカイト層の最大のネックがPbです。Pb を周囲にまき散らさないように安心・安全な製膜法を構築して低コスト化と環境に優しい太陽電池の実現に貢献したいと考えています。 以上の背景から、伊東研では下記に着目して研究を進めています。
・電子輸送層や電子バッファー層の材料利用率を高める、これらの製膜時の溶媒や加熱処理がペロブスカイト層に与える影響を無くす新手法を開発し、従来と同等以上の性能を実現しています。 材料を効率よく活用し、製造に必要な時間とエネルギーを1/10近くに削減することで環境とコストに優しい全塗布型の太陽電池を実現する。
・ペロブスカイト層製膜時のPbの飛散を極限まで減らした新規製膜法の開発、CBの消費量をまずは1/10に減らし、次の段階ではゼロにする工程の開発により、環境に優しい太陽電池を実現する。
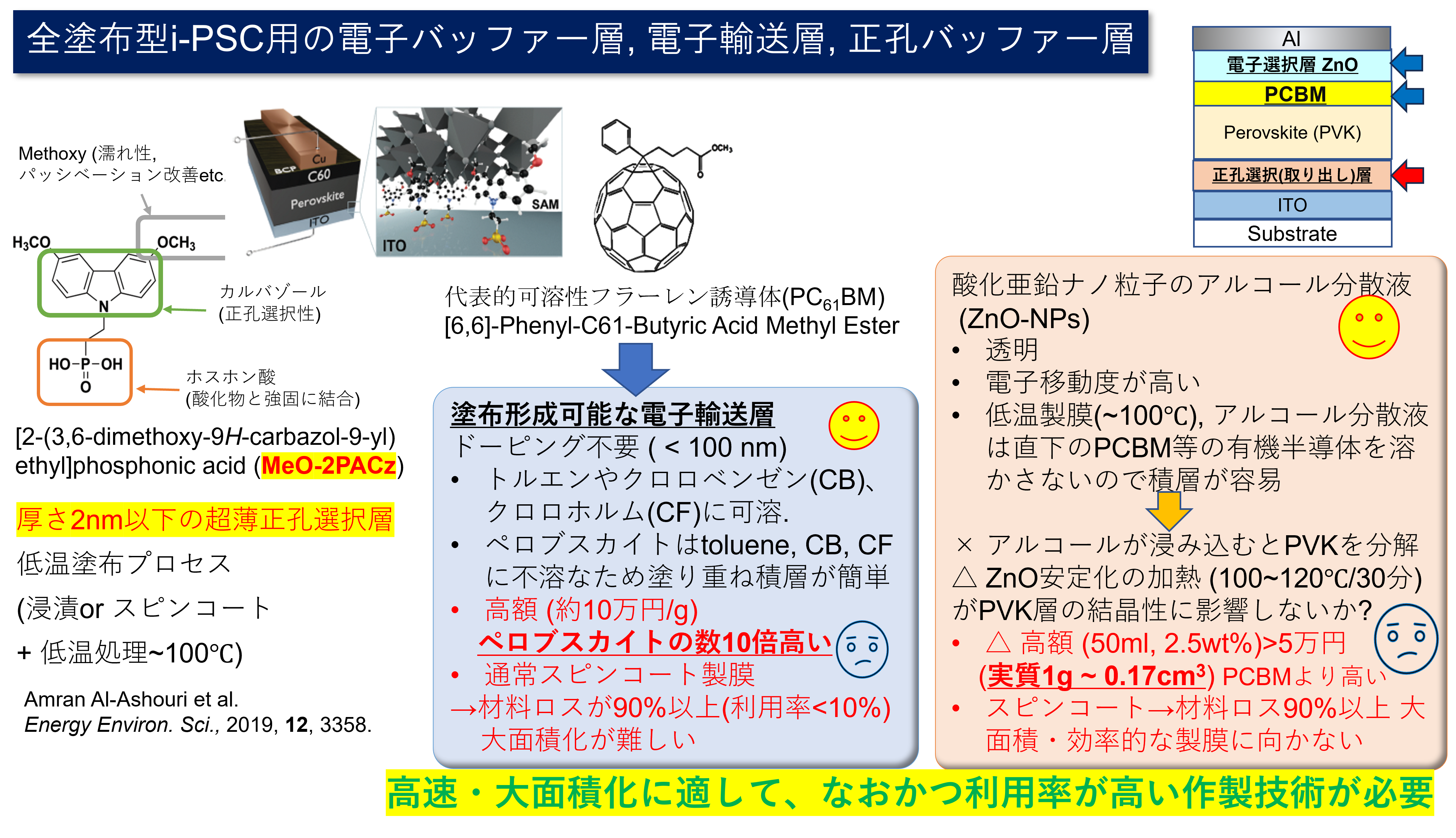
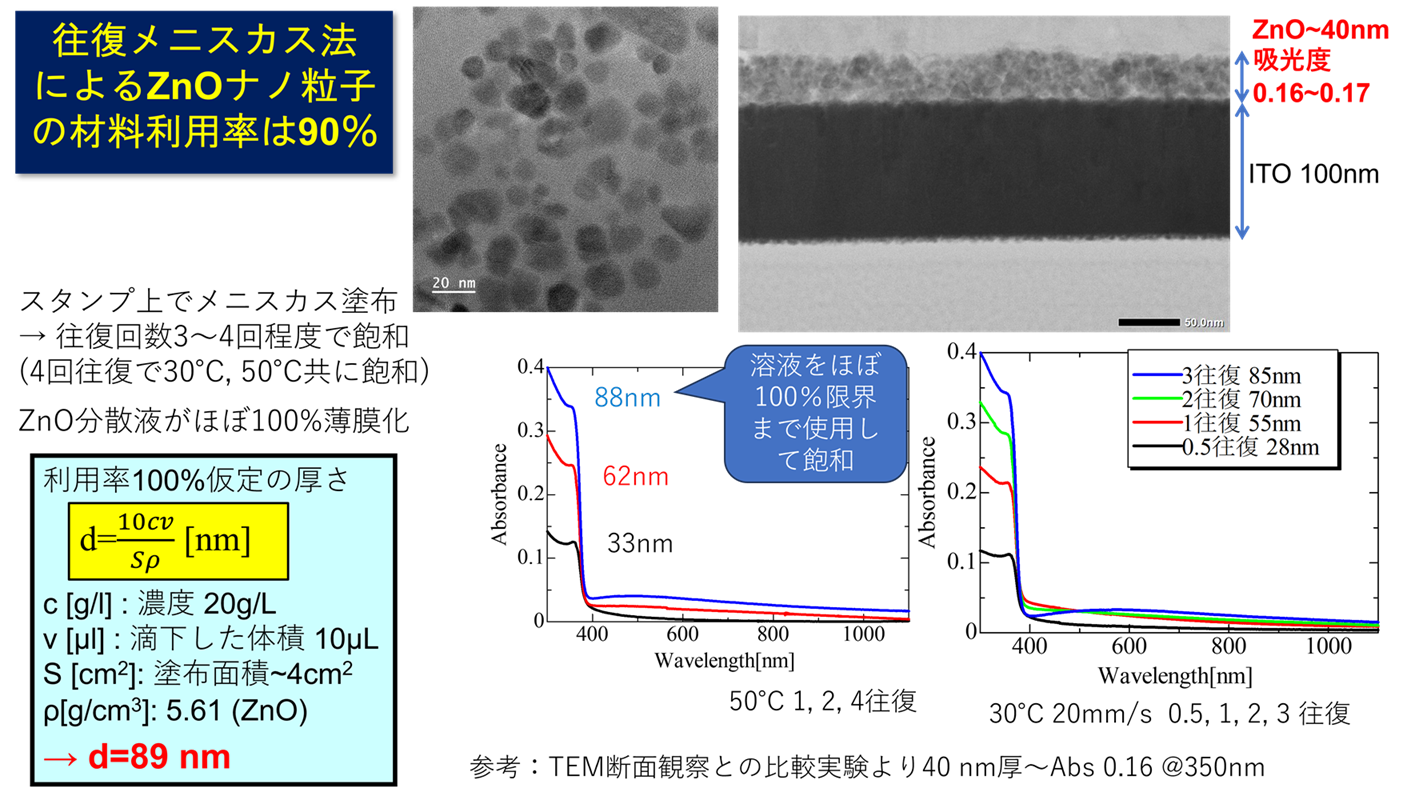
特に、IoTやAI技術の発展と連動してセンサはさまざまな機器やシステムに搭載され、年間1兆個のセンサが消費される時代が来ると推定されている(トリリオンセンサ)。そこで、重要なのが、小さくて高性能で、しかも安価なセンサである。
例えば、カーボンナノチューブやグラフェンと有機材料(主に高分子やゴム)を混合した複合材料を曲げたり引き伸ばすと、抵抗(R)や電気容量(C)が変化するので、動き(モーション)センサに活用できる。また、カーボンナノチューブ(CNT)はナノスケールの網目状構造を持つため、ガス透過性電極となる。そこで、水蒸気やガス状の化学物質によって電気的特性が変化する物質にCNTを電極として装着すると、高速・高感度なガスセンサの開発が可能となる。この他にも、グラフェンと有機機能材料を組み合わせた薄膜は高速な化学センサとなる。
伊東研究室では、耐熱性・化学的安定性に優れたポリイミドとカーボンナノチューブ(CNT)電極を組み合わせて、10msオーダーと従来の100倍高速な湿度センサや、グラフェン系薄膜(還元型酸化グラフェン/高分子ハイブリッド)のガスセンサ応用などの研究を行っています。
数10msで応答する湿度センサは、呼吸のモニタリングや人工呼吸器の高性能化にも有用で、動きに反応するセンサにも応用できることから、様々なシチュエーション(トレーニングや医療など)にも適用可能です。
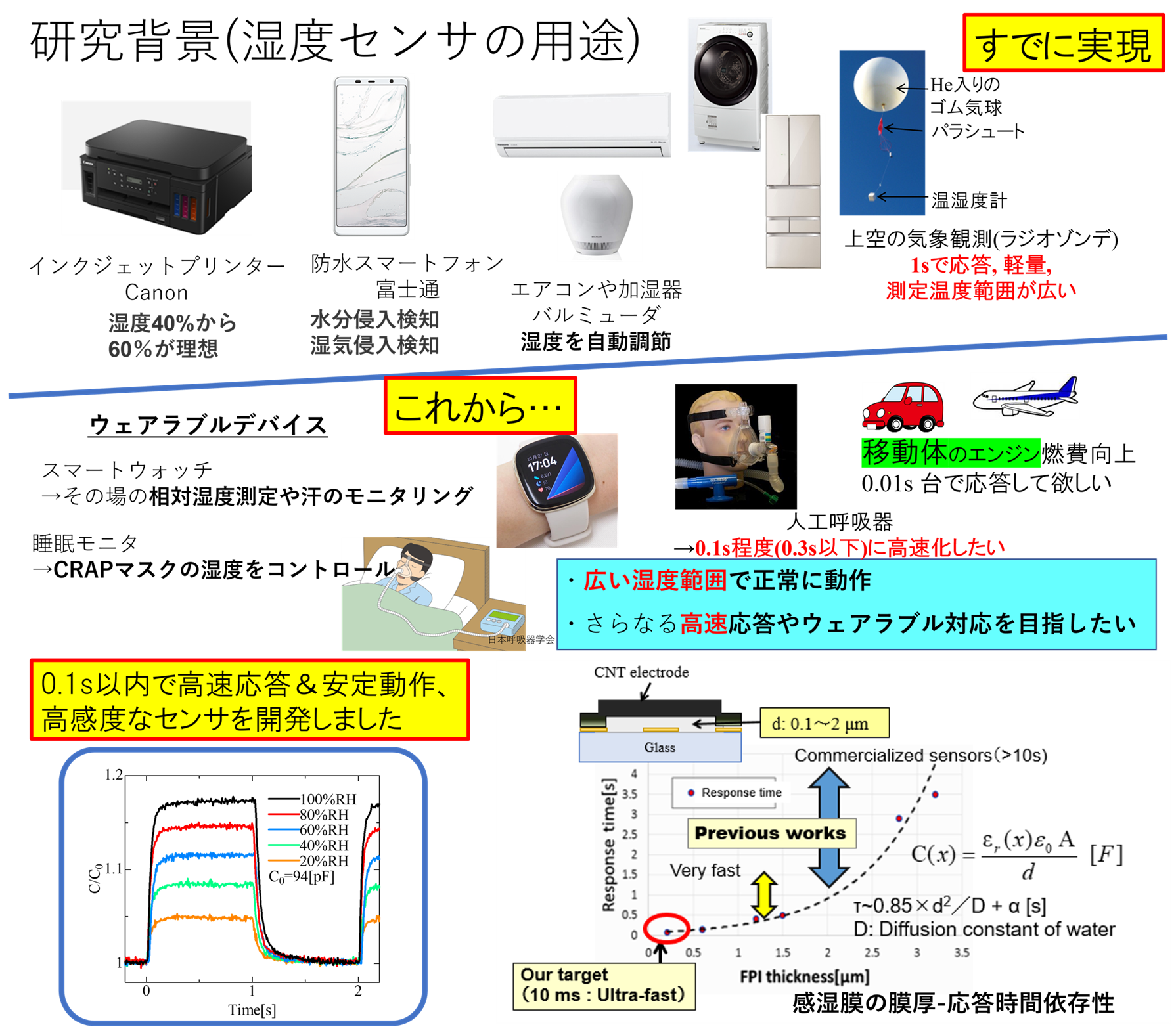
これからの当面の目標として、センサの高性能化や、CNTの配向制御と樹脂や伸び縮み可能な材料を融合した伸縮(歪み)センサの開発や、無線装置を連動したIoT用リアルタイム計測なども展開していきたいと考えています。
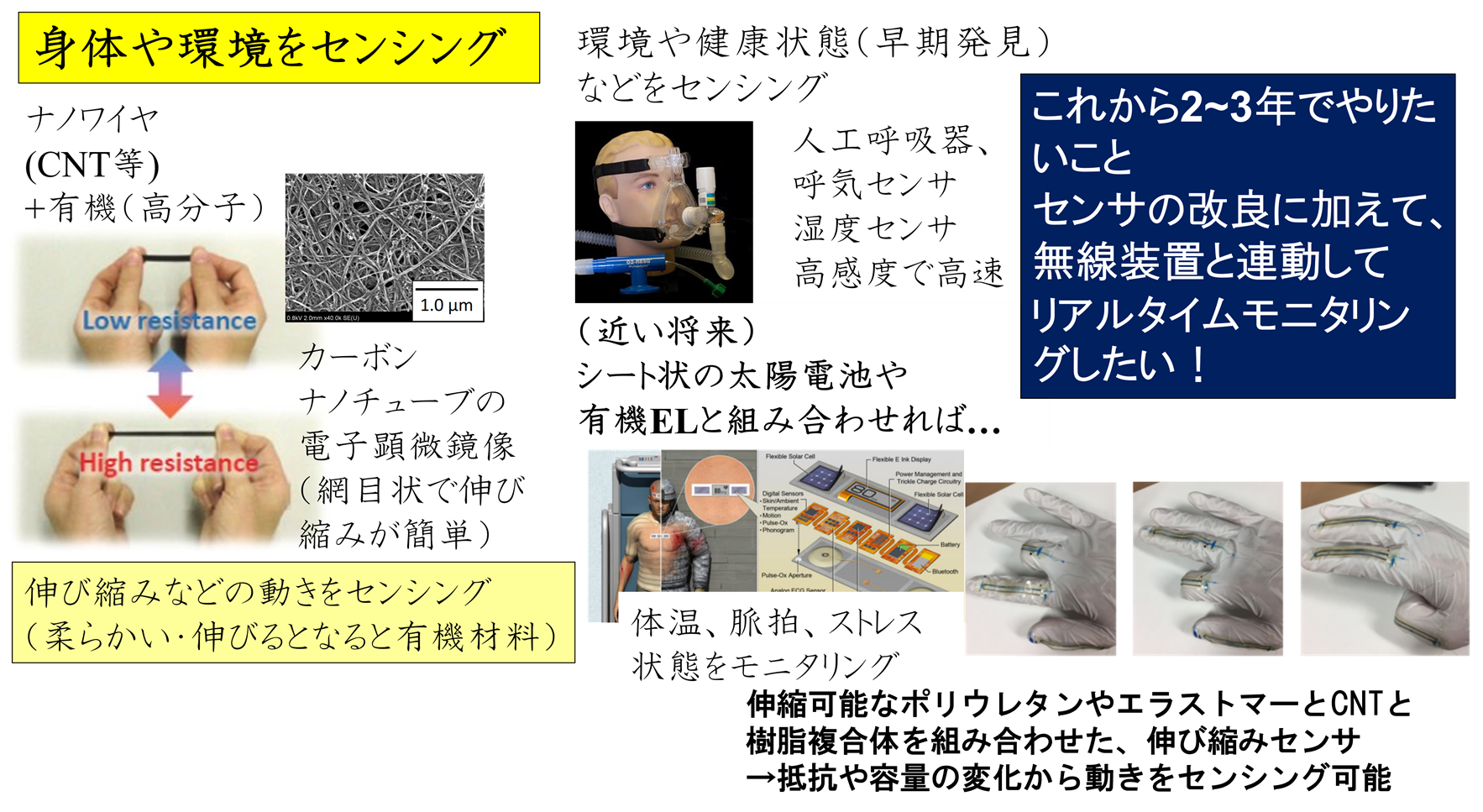
半導体集積回路に用いるトランジスタのゲート長となるテクノロジーノードを「2 nm 」プロセスで製品化する動きはすでに始まっている。
チャネル長は実際は10 nm以下にするのは難しいのが現状ですが、この距離はまさに大き目の有機分子や半導体量子ドットの大きさと重なります。
従来のSiに代表されるSiなどの無機半導体を微細加工するトップダウンプロセスは半導体そのものに大きなダメージを与えます。 近年注目が集まっているナノ材料の代表例にはMoS2やグラフェンなどの2次元物質もありますがを10nm以下に加工すると2次元材料としての機能を失う恐れも指摘されており、 縦・横・鷹さ方向全てが数nm以下のサイズに設計された欠陥の無い分子材料に期待が高まっている。
例えば、近年、目覚ましい性能向上を果たしてきた可溶性の有機半導体を例にとると、最初のFETの報告があった1980年代の10-6 cm2V-1s-1台だったものが、2020年代には 10~100 cm2V-1s-1までに向上している。この数値は、アモルファスSiをはるかに凌ぐが、結晶Siには及ばない。このため、マクロ(数μmを超えるサイズ)スケールで作製する場合は、速度面ではSi集積回路を超えることは難しく、有機材料ならではの超柔軟性を活かした応用を考えていくことが重要となる。
しかし、有機半導体分子や、半導体量子ドットのようにナノスケールで設計可能なナノ分子材料は、数nmのノードサイズにおいてこそ大きな可能性が期待される。マクロなスケールでは分子と分子(または量子ドットの間)の電子移動が遅いために移動度がSiに及ばないが、可溶性有機半導体は導電性を有する 1 nm程の大きさのコアと、可溶性を有する長さ1~2 nm の側鎖からなり、側鎖の末端を分子修飾すれば金属や酸化物に安定に固定することができる。 コアの移動度はグラフェン並み、すなわち Siをはるかに凌駕する(100倍以上)可能性を秘めており、次世代 2 nmプロセスと組み合わせることで、2030年代にはこれまでよりも桁違いに速くて高集積度(密度)の半導体デバイスの実現に有望な材料となる可能性がある。
また、分子コアに導体・半導体部位を組み込んだ半導体デバイスの他に、いわゆる有機分子固有の分極性部位と絶縁体部位を融合した有機誘電体分子1個からなる分子メモリーの実現の可能性もある。
このように有機電気電子材料に関する基礎科学的な研究、そこからもたらされる新しい応用の発想、概念は 「分子エレクトロニクス」という究極的なエレクトロニクス技術の開拓に貢献し、電気電子工学・ 産業分野に画期的な飛躍をもたらすものとして期待される。
伊東研では、横方向のサイズはまだまだマクロなサイズだが、厚さ方向には数nmの極薄の分子材料を用いたトランジスタやメモリーデバイスの研究を行ってきました。
超微細なナノデバイスは単独の研究室では難しい課題ですが、ナノ分子材料が単体で有する光・電子機能を引き出すのはこの分野の夢でもあります。
予算と共同研究者とのコラボが必要になりますが、近い将来、分子エレクトロニクスに貢献できる研究ができれば、面白いと思いますね。
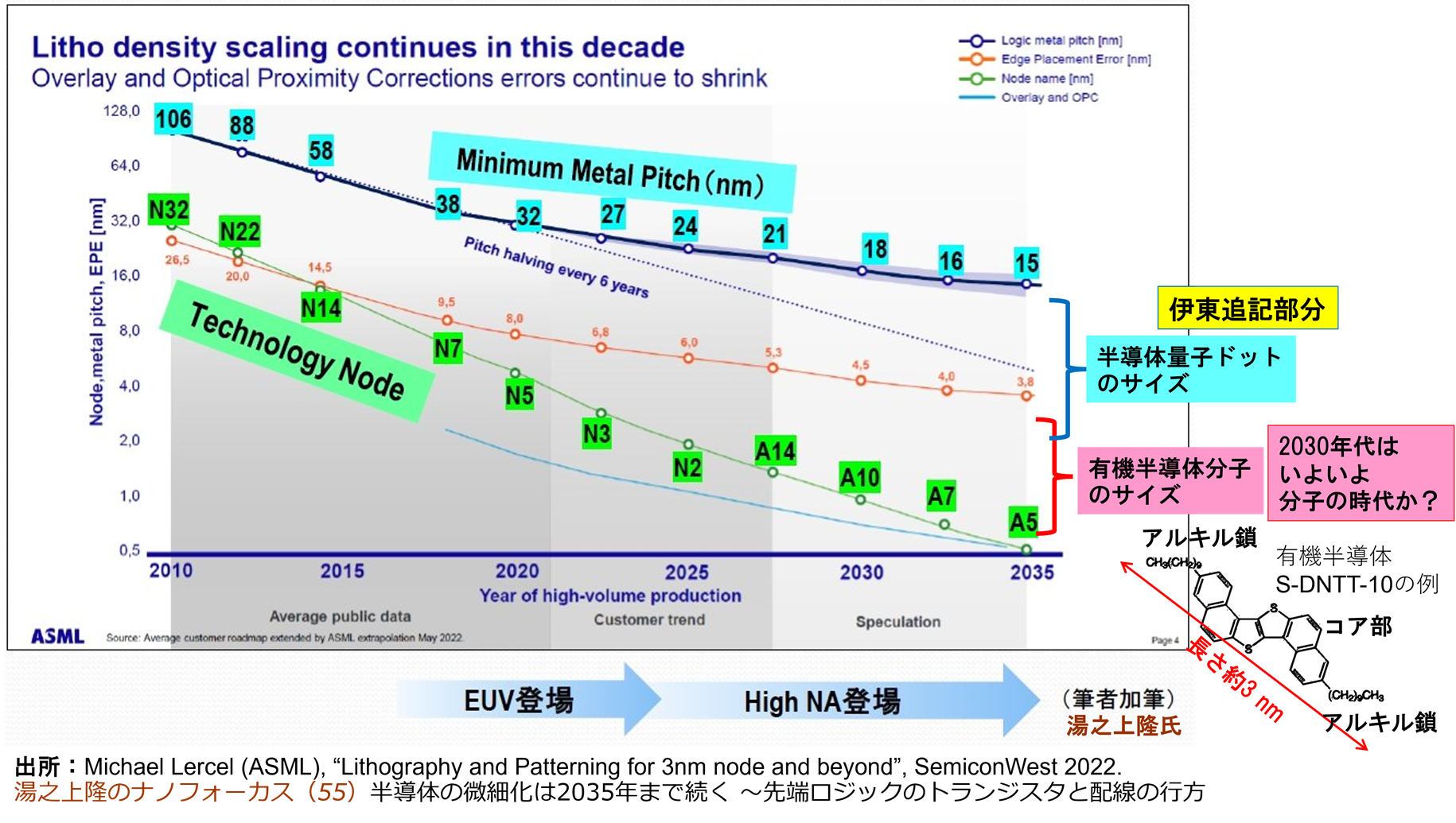